Skills Development for Additive Manufacturing
Additive technology has become common in manufacturing. We’ve had 3D printing at Design Ready Controls for years now, using it to improve our techniques and expand our capabilities. As 3D printing advances, operators need to address more variables—and to get the greatest benefit from additive technology, manufacturers should invest in skills development for operators.
Production Value of Additive Manufacturing
Prototypes from outside vendors can be expensive, with long lead times. They’re often made from metal and require casting, milling or other expensive processing. That can be time consuming, especially if the first prototype doesn’t meet requirements. Additive manufacturing can do a comparable job in less time and for less money. The same principles apply to creating one-off products like models, fixtures, holders and simple tools. We can 3D print many of them at a lower cost than they are commercially available, and customize them to our specifications.
Even if the end product needs to be metal, printing a proof of concept in polylactic acid (PLA) filament can be useful. We can design and print a prototype, test it for usability, and make any necessary changes to form or function before sending out the model for machining or casting.
Skilled operators add value to manufacturing by designing and printing cost-effective prototypes and custom tools and fixtures.
Adjusting for Variables
The additive manufacturing process is more than just supplying a digital design and hitting PRINT. A lot of variables need to be considered, and a skilled operator can help get the best results. Operators can balance the multiple variables and model features, calibration, filament variation, end use of product and more. To get where we are now has taken a lot of work, but the time was well spent.
Our four 3D printer models—two Makerbot 5th Generations, one Ultimaker3, and a Mark 2 by Markforged—all have their own software, hardware and filament that affect their final prints.
Skilled operators have experience with many trial and error prints and can recognize and adjust for multiple variables.
Calibrating for Accuracy
Each 3D printer model will print a little bit differently, making calibration an important part of the overall process. We use prints of 3DBenchy—an industry standard, open source design of a boat—to test dimensional accuracy, tolerances, and warping of the final print. Heating plastic from solid to its transitional state as liquid means the prints need to cool to solidify. A significant amount of print shrinkage has to be taken into account.
Measuring the dimensions of the final print reveals any discrepancies between the digital file and the physical output. Troubleshooting is a critical part of the process, and it can mean a lot of trial and error.
Skilled operators can reduce calibration time for accurate prints, leaving room for innovation.
Filament Choices
Each filament has unique properties and best practices. Our Ultimaker3 prints with standard PLA filament, and the Mark 2 can print high strength materials like their signature, carbon-fiber Onyx or other carbon fiber and Kevlar blends. Several filaments are among the most commonly used:
- Polylactic acid (PLA): common, plant-based, biodegradable thermoplastic of medium durability
- Polycarbonate (PC): strong, impact resistant filament with flame retardant properties
- Thermoplastic elastomers (TPE): flexible, rubber-like filaments with impact resistance
- Polylvinyl Alcohol (PVA): water soluble and used for temporary support structures
- Nylon: strong, flexible and durable, similar to the plastic of water bottles
- Acrylonitrile Butadiene Styrene (ABS): ductile, durable and resistant to heat and UV damage
Besides these common filaments, development continues on other additive manufacturing materials. Concrete and ceramic are becoming popular materials for home construction and fixtures. Titanium, aluminum and stainless steel is used in the aerospace and automotive industries. Kevlar and carbon fiber blend filaments provide high-durability prints for a variety of industrial uses. Wood-infused PLA filament is used to achieve a certain look, as are color-changing and glow-in-the-dark filaments.
Such a wide range of filament choices also means a wide range of filament prices. Some materials cost 10 times as much as others, which has to be considered along with a print’s form, function and durability.
Skilled operators consider the best 3D printer, filament cost and properties for the desired end print.
Print Orientation
The 3D printers at Design Ready Controls use fused deposition modeling (FDM), meaning materials are laid down in layers. The weakest points in any print are where one layer meets another. Any bending, twisting or flexing forces will stress those points. It’s important to understand how the final print will be used, and how outside forces will affect the finished design. Changing the orientation of a print alters its ability to withstand those outside forces.
Skilled operators adapt print orientation to maximize layer strength and make the best use of the chosen filament.
Continuous Skill Development
Part complexity, inlays, material combinations, tolerances, print bed adhesion, and printer hardware and software all affect the quality of the final print. And these are only a few of the 3D printing variables an operator has to consider. Manufacturers who want to take advantage of the value provided by 3D printing should provide opportunities for operators to continuously develop their skills.
Having a certain degree or certificate doesn’t guarantee success for a 3D printer operator, but continuous education will. The technology is changing all the time. Makers of 3D printers are continuously developing new capabilities, and filaments are evolving, too. You always have to be ready to try and fail and try again—to take on a new challenge even if the last print looked like a plate of hairy spaghetti.
Taking a completely digital design—almost an imaginary object—and making it into something real that you can hold in your hands isn’t always easy, but it’s really rewarding. That’s why working in manufacturing and 3D printing is so amazing and satisfying. You start with an idea and get to make it real.
Skilled operators know the value of additive manufacturing and continue to develop their talents as new challenges arise.
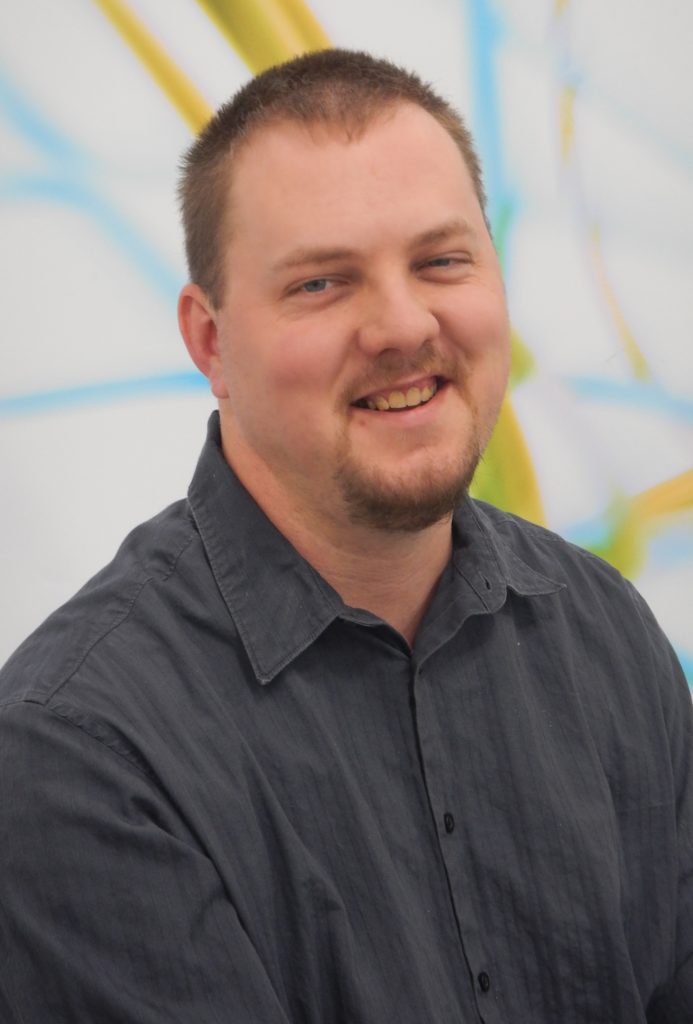