How We Do It – Ramp Up Plans
Ramp-Up Plans
Design Ready Controls’ standard process is to meet our customer requirements through the design, implementation, and execution of a production ramp-up plan. Production ramp-up plans connect customer orders to Design Ready Controls infrastructure, design, parts, and people over a defined period of time. The plans contain defined milestones that ensure the assembly of completed control panels matches our OEM customer’s production requirements of finished equipment.
Design, Implement and Execute
Design: Ramp-up plans are designed to successfully execute customers’ desired order dates and are based on specific activities required to be successful in infrastructure, design, parts, and people.
Implement: Assign a project manager, develop project plan, host kick-off meeting, and define milestones and reporting cadence.
Execute: Track progress through leading indicators in each project segment, work issues in severity ranked order as they arise, and report progress weekly to customers.
Why is this Important?
Output: Production ramp-up plans convert orders to output of completed control panels.
Visibility: Production ramp-up plans offer our customers direct visibility to issues, opportunities, and progress towards defined milestones. By checking progress along the way of a ramp-up plan we reduce uncertainty and work together to pace our output to what our customer requires
Alignment: Designing, implementing, and executing a production ramp-up plan together, eliminates the waste of over-production or under-production by matching Design Ready Controls’ output to OEM customers’ production requirements of finished equipment.
In Closing
As a contract manufacturer of electrical control panels we have the amazing opportunity to service many high-growth markets. This opportunity creates the responsibility to respond to the requirements of growth well. Successfully designing, implementing, and executing ramp-up plans represent the foundation of our response.
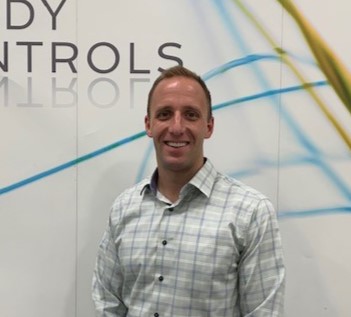