Digital Twins Win
The Value of a Digital Twin
A digital twin is a virtual model of a physical asset. The digital version mirrors the real-world item. At Design Ready Controls, we decided to use the digital twin concept to help improve our internal systems and provide customers with better results and service.
The physical asset in this case is a control panel, with a 1:1 relationship between the virtual space and what is on our production floor. We use the ePLAN p8 and ProPanel software suite, along with a structured database that contains all information for components, schematics, and 3D representations. We use that information to build a 3D model of the panel, route the wiring, and generate reports needed to build the panel—bill of materials, wire reports, and information for our Perforex and Komax machines.
Using a digital twin, we can manipulate, view, and critique a panel within the virtual realm before documentation is released to the production floor. This allows us to look at things such as clearance between components in the 3D space, interference between parts, wire bending radiuses, and the spacing around components required for heat dissipation. All of this is done up front and because of this, we can alleviate potential issues before it hits the production floor.
Structured Database: Single Source of Truth Method
The concept behind the database is to utilize this as the Single Source of Truth (SSOT). A structure where information is only stored once and all references to these components are linked back to this database. Any update to the database is reflected everywhere else that information is used, eliminating the possibility of duplicated or outdated information. This assures all projects are utilizing the most up to date information.
New System, New Challenges
Adapting to a new system can mean there will be challenges on the front end. We’ve invested heavily in training both on and off-site due to the learning curve and having to utilize the higher level functions within ePLAN.
One of the biggest challenges in implementing a digital twin has been the database and inputting the component information. We are having to add an extensive amount of detail, which can be a lot of work, but once it’s completed it’s not necessary to do it again. Although this manual input is tedious, the benefits greatly outweigh the time taken to complete it.
Real World Benefits Today
We strive for clear communication and responsive customer service; using a digital twin helps with both. Before implementing this method, customer communication was often based off two-dimensional drawings and schematics. This opens the door to potential issues such as component alignment or space constraints being found during the manufacturing process and causes delays and unnecessary rework. Now we can identify those kinds of concerns right away and communicate this with the customer in a more proactive manner. Digital twin technology allows us to provide detailed information before anything is built.
More Advantages Tomorrow
We are already looking for ways to add this higher level of detail to our Automated Panel Expert (APE), providing benefits to long-standing customers as well as new ones. The use of a digital twin is iterative; it can only get better; any future utilization is going to see improvements.
As the data stream becomes more automated, what is produced in the digital space will be represented more precisely on the production floor. So, down the road, robots and other machines can be added to our manufacturing process and driven by digital twins.
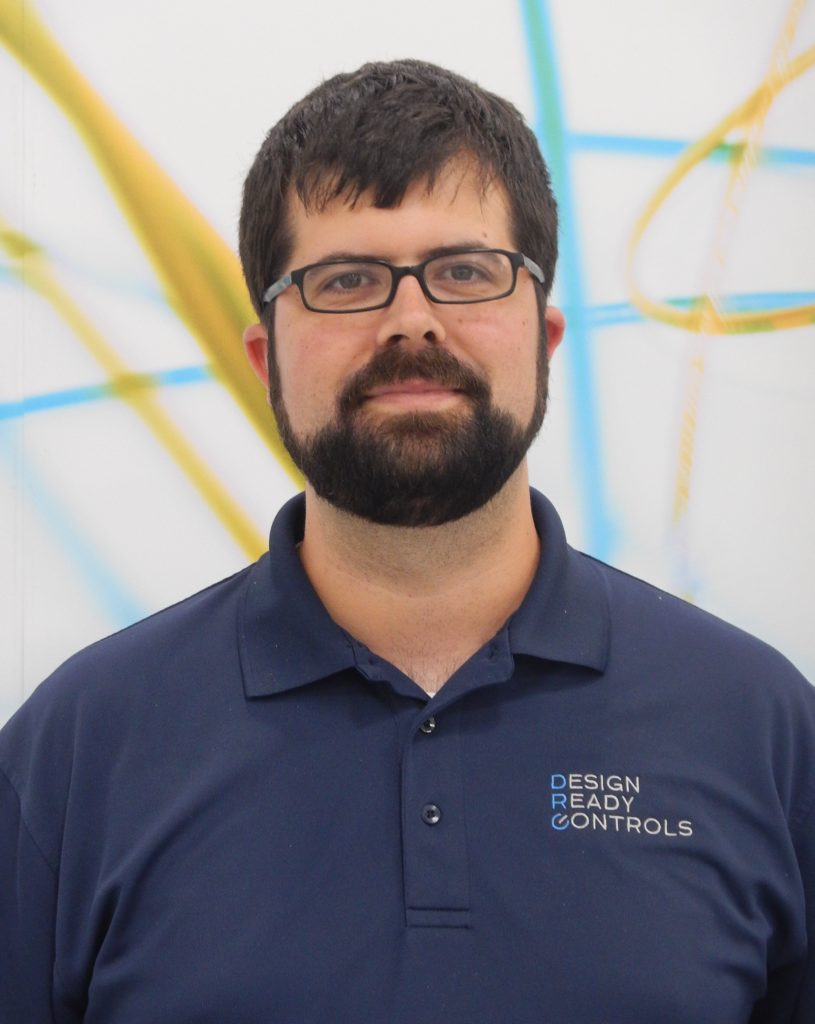